KEW Foundries has supplied sheave wheels to the Shaft Sinkers group, to be used on a project being conducted for the global chemical giant – EuroChem. The sheave wheels form part of the winder installation which will transport personnel, material and waste rock during the sinking phase. The project, located at EuroChem’s Gremyachensky mine, in the Kotelnikovo district of the Volgograd region in Russia, will mine the Gremyachskoye deposit – one of the largest deposits of potash in the world. The shaft will be seven metres in diameter with a final depth of 1120 metres.
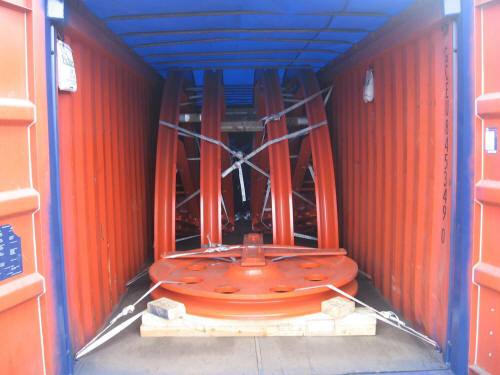
Extreme care has been taken when packing sheave wheels destined for EuroChem’s Gremyachensky mine to ensure that the products reach their destination safely and conform to stringent Russian shipping regulations.
KEW Foundries worked in conjunction with Mining and Engineering Technical Services (METS), the in-house design division of the Shaft Sinkers group, to design and develop the sheave wheels for the project. In total, 15 sheave wheels have been supplied with external diameters ranging from 1372 mm to 4876 mm.
Petra Dippenaar, Group Procurement Manager, Shaft Sinkers, says that the quality of workmanship and the highly competitive prices offered by KEW Foundries makes the company a preferred provider when selecting a sheave wheel supplier. “We have worked with KEW Foundries on a number of projects in the past and, to date, we have never been disappointed with the products that have been supplied. KEW Foundries have consistently supplied solutions which meet our extremely high safety requirements, and we feel that for projects of this magnitude, it is vital to use products which can be trusted to deliver the highest degree of safety possible.”
KEW Foundries’ sheave wheel solutions are also competitively priced, Dippenaar explains: “When we first started to approach the Gremyachensky project, we expected to source a lot of the necessary equipment from Russia and neighbouring countries. However, we found that mining products across the board can be sourced far more cost-effectively in South Africa. South African products, surprisingly, are still cheaper, even when you factor in the high costs of shipping. KEW Foundries’ sheave wheels are no exception to this rule.”
Shaft Sinkers has gone to extensive lengths to ensure that equipment destined for the Gremyachensky mine reaches its destination safely. This includes moisture protection, shrink wrapping, and extensive strapping and padding within the 50 containers and twenty break bulk crates which are being transported to site. Documentation, including shipping documents, needed to be transcribed into both English and Russian, in order to meet stringent Russian custom requirements. These measures enable cargo to travel safely on its 42 day sea voyage to the port of Novorossiysk. The cargo also needs to survive an arduous 20 days of customs clearance and road travel to reach its final destination.
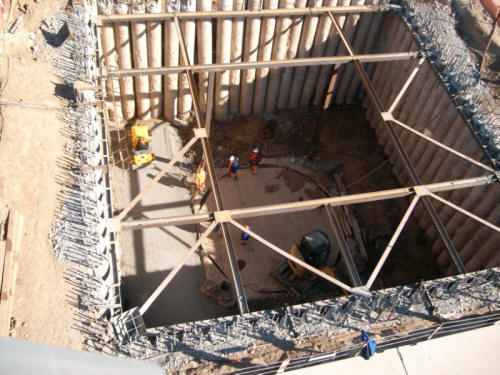
EuroChem’s Gremyachensky mine will have a final depth of 1120 metres – making it one of the deepest potash mines in the world.
“As a result of the extremely long shipping distances and lead times involved, damaging the contents of just one container, could delay the entire project,” says Dippenaar.
Work for main sink will commence early next year. The project is expected to be completed in four years time.